Ensuring patient safety is a fundamental principle in healthcare delivery, and medical equipment maintenance plays a pivotal role in achieving this goal. In Uganda, where access to quality healthcare is essential, adopting best practices in medical equipment maintenance is imperative to safeguarding patient well-being and optimizing healthcare delivery. This article delves into the importance of comprehensive medical equipment maintenance, highlighting key strategies, considerations, and examples tailored to healthcare.
The Importance of Medical Equipment Maintenance
Medical equipment maintenance is paramount in the healthcare industry. The following points illustrate its significant role:
Patient safety: Effective medical equipment maintenance is crucial for ensuring precise diagnosis, treatment, and monitoring of patients. Equipment failure can result in inaccurate readings, misinterpretations, or errors in treatment, putting patient safety at risk and compromising their well-being.
Reliability and performance: Ensuring the reliability of healthcare equipment is imperative for providers to deliver high-quality care effectively. Consistent maintenance is essential to guaranteeing that medical devices are functioning at their best, thereby minimizing the potential for malfunctions or mistakes during critical medical procedures.
Cost-efficiency: Regular maintenance is essential for preventing expensive repairs or replacements by addressing minor issues before they become significant problems. It also helps prolong medical equipment’s lifespan, maximizing the return on investment for healthcare facilities.
Patient experience: Patients are increasingly expected to receive top-tier care incorporating current and dependable equipment. Well-maintained equipment improves the patient experience and contributes to precise diagnoses, effective treatments, and improved overall results.
Operational efficiency: Properly maintained equipment plays a crucial role in the efficient functioning of healthcare facilities. It helps minimize interruptions in patient care, reduce downtime, and enable healthcare providers to concentrate on delivering high-quality and effective treatments.
Preventive measures: Maintenance activities often include preventive measures to identify and address potential issues before they impact patient care. This proactive approach helps prevent equipment failures and ensures continuous service availability.
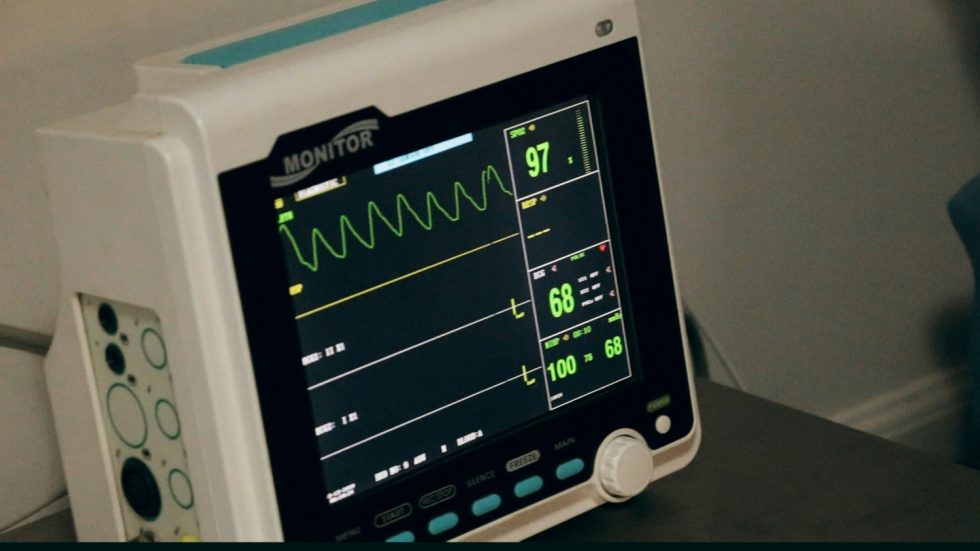
Regular inspection and testing: Regular and functional assessments are vital in identifying potential issues or defects in medical equipment. For example, routine calibration checks on vital sign monitors ensure accurate readings, thus minimizing the risk of misdiagnosis or improper treatment. In healthcare facilities in Uganda, blood pressure monitors are inspected monthly to verify their accuracy and functionality. Any deviations from standard readings trigger immediate calibration or servicing.
Preventive maintenance scheduling: Creating and following a preventive maintenance schedule is essential for maintaining equipment and proactively preventing unexpected downtime. Consistent cleaning, lubrication, and calibration are critical factors in extending the lifespan of medical equipment and maintaining optimal performance. Healthcare facilities must adhere to manufacturer guidelines for servicing anesthesia machines every six months. Implementing a preventive maintenance strategy dramatically minimizes the likelihood of equipment failure during crucial surgical procedures.
Staff training and education: It is imperative to implement thorough training programs for healthcare personnel regarding the operation of equipment, maintenance protocols, and safety procedures. This is crucial for handling and maintaining medical equipment effectively. Well-informed staff can promptly identify and address maintenance issues, reducing the risk of adverse events.
For instance, regular training workshops on ventilator maintenance should be organized for healthcare staff. These workshops should include hands-on sessions to improve staff competency and confidence in managing critical equipment.
Documentation and record-keeping: It is crucial to keep precise records of maintenance activities, such as dates, tasks performed, and any repairs or replacements, to track equipment history and adhere to regulatory requirements. Utilizing centralized documentation systems allows easy access to maintenance records and enables efficient auditing or inspections. Electronic maintenance logs for autoclaves are necessary for healthcare facilities throughout Uganda to document sterilization cycle maintenance procedures and ensure compliance with infection control standards.
Environmental factors management: It is vital to ensure that medical equipment is stored and operated in environments that meet the proper environmental conditions, including temperature, humidity, and ventilation. These factors are crucial in maintaining the equipment’s integrity and functionality. Adequate storage and operational settings help protect the equipment from potential damage caused by external factors such as dust, moisture, or electrical irregularities.
For example, ultrasound machines in Ugandan healthcare facilities should be stored in temperature-controlled rooms to prevent overheating and guarantee optimal performance during diagnostic procedures.
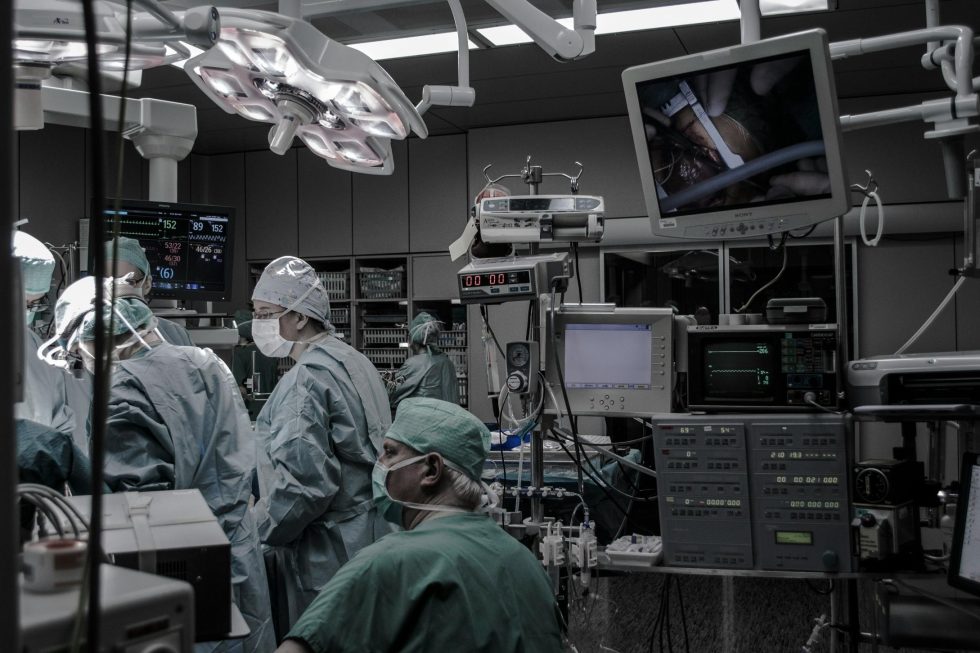
Conclusion
Effective medical equipment maintenance ensures patient safety, improves healthcare quality, and maximizes operational efficiency in Uganda. By utilizing proven best practices tailored to the local environment, healthcare facilities can guarantee their medical equipment’s dependability, precision, and durability. Heritage Plus Supplies is dedicated to supporting these endeavors by offering top-notch equipment, expert maintenance services, and customized solutions designed to address the distinct requirements of healthcare providers and patients throughout Uganda.